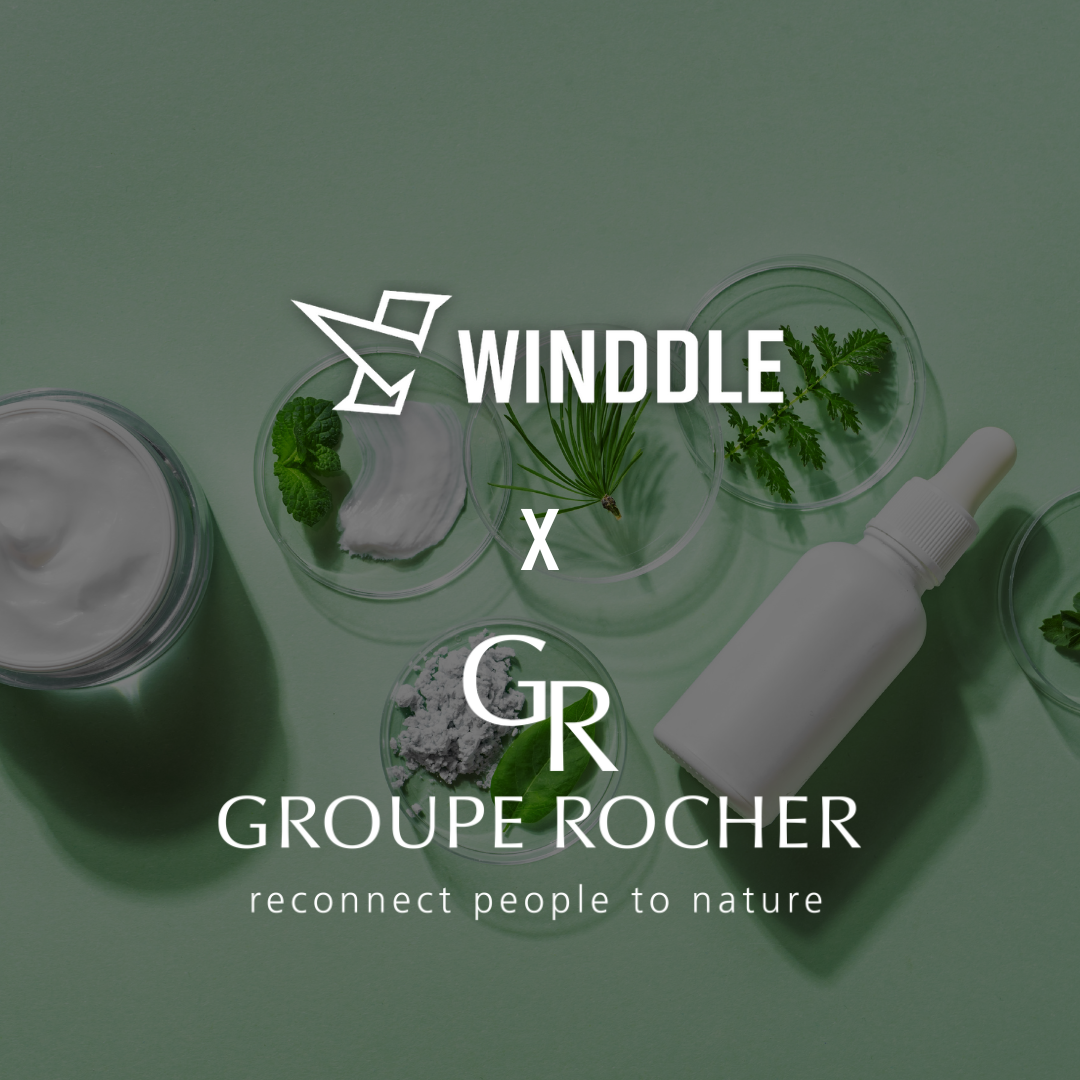
Winddle Supports the Transformation of the Purchasing & Supply Chain Processes at Groupe Rocher
.jpg)
The Operations branch of Groupe Rocher, a leader in the cosmetics industry, has chosen Winddle, a collaborative Supply Chain Management platform, to enhance its supplier relationships and supply chain management.
In 2021, the group initiated a plan to overhaul its ERP and forecasting tool (SAP) by defining a Business Core Model, which includes new supplier collaboration processes for procurement. Winddle is playing a key role in this digital and operational transformation by providing its expertise and technology to support Groupe Rocher.
Founded in 1959, Groupe Rocher is a major player in the cosmetics sector both in France and internationally, with brands such as Yves Rocher, Arbonne, and Dr. Pierre Ricaud. As a family-owned company established in Brittany with a directly managed production facility, Groupe Rocher develops, produces, and distributes its makeup and skincare lines.
“The implementation of Winddle as a collaborative supplier platform is part of the transformation of our procurement practices. The goal is to refocus the role of the buyer on the relationship with the supplier, with a greater emphasis on managing and securing supply needs, within a framework provided by the Purchasing department,” says Gladys Pouteau, Business Project Manager.
The platform is scheduled to launch for the first suppliers in October, with the objective of automating processes and freeing buyers from administrative tracking tasks, which are currently largely managed through Excel. This will also provide better visibility over the supply portfolio and enable more effective sharing of forecasts with suppliers to monitor production progress. The project also aims to have structured business data and reliable, precise performance indicators to share with suppliers and the purchasing team.
“We are an industrial group,” explains Bertrand Masson, Supply Chain Director of Groupe Rocher. “Our procurement involves numerous firm purchase orders, of course, but also forecasts, where it is important for suppliers to have visibility and be able to commit so that we can secure our production plans and supply timelines.”
The project, supported by Winddle, covers 95% of the procurement orders (packaging, raw materials, and technological subcontracting) for the Operations division of the group, involving 150 suppliers, primarily in France and Europe, and around thirty internal employees, including buyers and transport managers.
“With lead times that can range from 3 weeks to several months, mastering our planning, ensuring smooth collaboration with our suppliers, and achieving the associated gains in agility and efficiency are key to the performance of our production sites in Brittany,” emphasizes Bertrand Masson.
“We were convinced by the adaptability of Winddle’s solution,” explains Gladys Pouteau. “The platform will allow us to meet both our current and future identified needs. We know that business processes evolve quickly, so it is essential for us to rely on a partner capable of supporting us effectively and providing the necessary flexibility to adjust our collaboration processes, operational alerts, and key performance indicators.”
Emilia Jevakhoff, CEO of Winddle, concludes: “We are delighted with the trust that Groupe Rocher has placed in Winddle to support the transformation of its Purchasing & Supply Chain processes. We are thrilled to work closely with Groupe Rocher to foster agility, collaboration, and operational excellence in industrial procurement.”