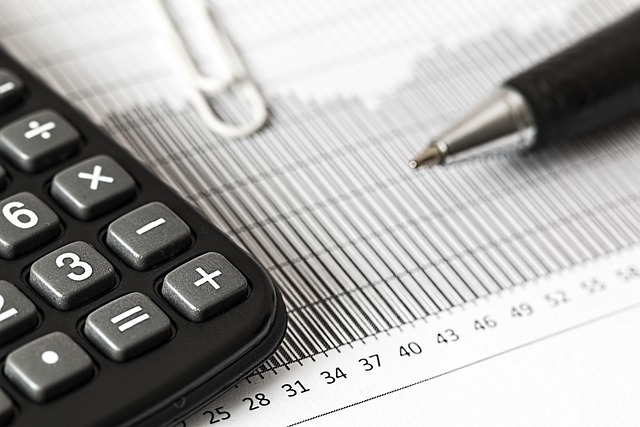
OTIF and Other Logistics KPIs
Efficient supply chain management relies on clear, actionable metrics. Among these, OTIF – "On Time In Full" – stands out because it captures two critical dimensions of delivery performance: timeliness and completeness. But how does OTIF stack up against other logistics KPIs? Let’s take a closer look.
What Is OTIF?
OTIF measures the percentage of orders that are delivered both on time and in full. It’s calculated as follows:
OTIF (%) = (Number of orders delivered on time and complete ÷ Total number of orders) × 100
This metric offers a comprehensive view of service quality by addressing:
- Timeliness: Are orders arriving on the agreed-upon date?
- Completeness: Are the orders delivered with every item included?
How OTIF Compares to Other Logistics Indicators
OTIF vs. On-Time Delivery (OTD)
While OTD focuses solely on the punctuality of deliveries, OTIF adds a crucial layer by ensuring the order is also complete.
- OTD’s Strength: Its simplicity makes it easy to measure whether deadlines are met.
- OTD’s Limitation: An order might be delivered on time but still be incomplete.
- OTIF’s Advantage: By combining both factors, OTIF provides a fuller picture of customer satisfaction.
OTIF vs. Service Level
Service level metrics typically gauge a company’s overall ability to meet customer expectations. These may include multiple factors like timeliness, order accuracy, and inventory availability.
- Service Level: Often broken down into several sub-indicators, offering insights into different operational areas.
- OTIF: Zeroes in on the dual requirements of promptness and order completeness, making it a powerful standalone indicator for pinpointing operational issues.
Other Key Metrics
While OTIF is essential, it works best when used alongside other performance indicators:
- Order Accuracy: Measures the percentage of orders without errors—critical for reducing costly returns and boosting customer trust.
- Order Cycle Time: Tracks the duration from order receipt to delivery, helping to uncover process bottlenecks.
- Picking Error Rate: Highlights issues in warehouse order preparation, which can directly impact OTIF scores.
- Lead Time: Captures the total time taken from order receipt to final delivery, offering insight into overall process efficiency.
Advantages and Limitations
The Strengths of OTIF
- Holistic Overview: By combining timeliness and completeness, OTIF provides a clear snapshot of logistical performance.
- Customer Focus: High OTIF scores are strongly correlated with improved customer satisfaction and loyalty.
- Diagnostic Power: A dip in OTIF quickly signals potential issues—whether in order preparation, inventory management, or transportation—prompting timely corrective actions.
Considerations to Keep in Mind
- Data Collection Complexity: Calculating OTIF accurately requires integrating data from various systems (ERP, WMS, CRM, etc.).
- Sector Variability: What’s considered an excellent OTIF score can vary widely between industries. A 95% score might be outstanding in one sector and merely average in another.
- Complementary Use: No single KPI tells the whole story. Pairing OTIF with other metrics gives a more complete picture of supply chain performance.
Choosing the Right Metrics for Your Business
Your choice of KPIs should align with your specific objectives and operational challenges:
- For a comprehensive view of customer satisfaction, OTIF is indispensable.
- If on-time performance is your primary concern, then OTD or overall service level metrics may suffice.
- To diagnose warehouse efficiency, focus on order accuracy and picking error rates.
By adopting a multi-metric approach, you can gain a 360° view of your supply chain performance. This comprehensive insight enables you to implement targeted improvements that not only enhance operational efficiency but also elevate customer experience and competitiveness.
Conclusion
OTIF shines by capturing the dual imperatives of delivering on time and in full. While it offers a robust measure of logistic efficiency, it’s best used in conjunction with other KPIs—such as OTD, service levels, order accuracy, and cycle times—to provide a detailed understanding of your operations. With the right combination of metrics, you can identify precise improvement areas, streamline your processes, and ultimately transform logistical challenges into opportunities for growth.
Embracing a holistic KPI strategy is key to building an agile and effective supply chain that meets customer demands in today’s fast-paced market.